The introduction of the Redledge system, a fully automated inventory stock management system, alongside our established national logistics network puts SL+5 at the forefront of retail parts distribution. This system manages over 50,000 SKUs, bar codes, and QR codes, allowing SL+5 to better support SL+1 in maintaining an equipment availability of over 99%.
KEY UPDATES
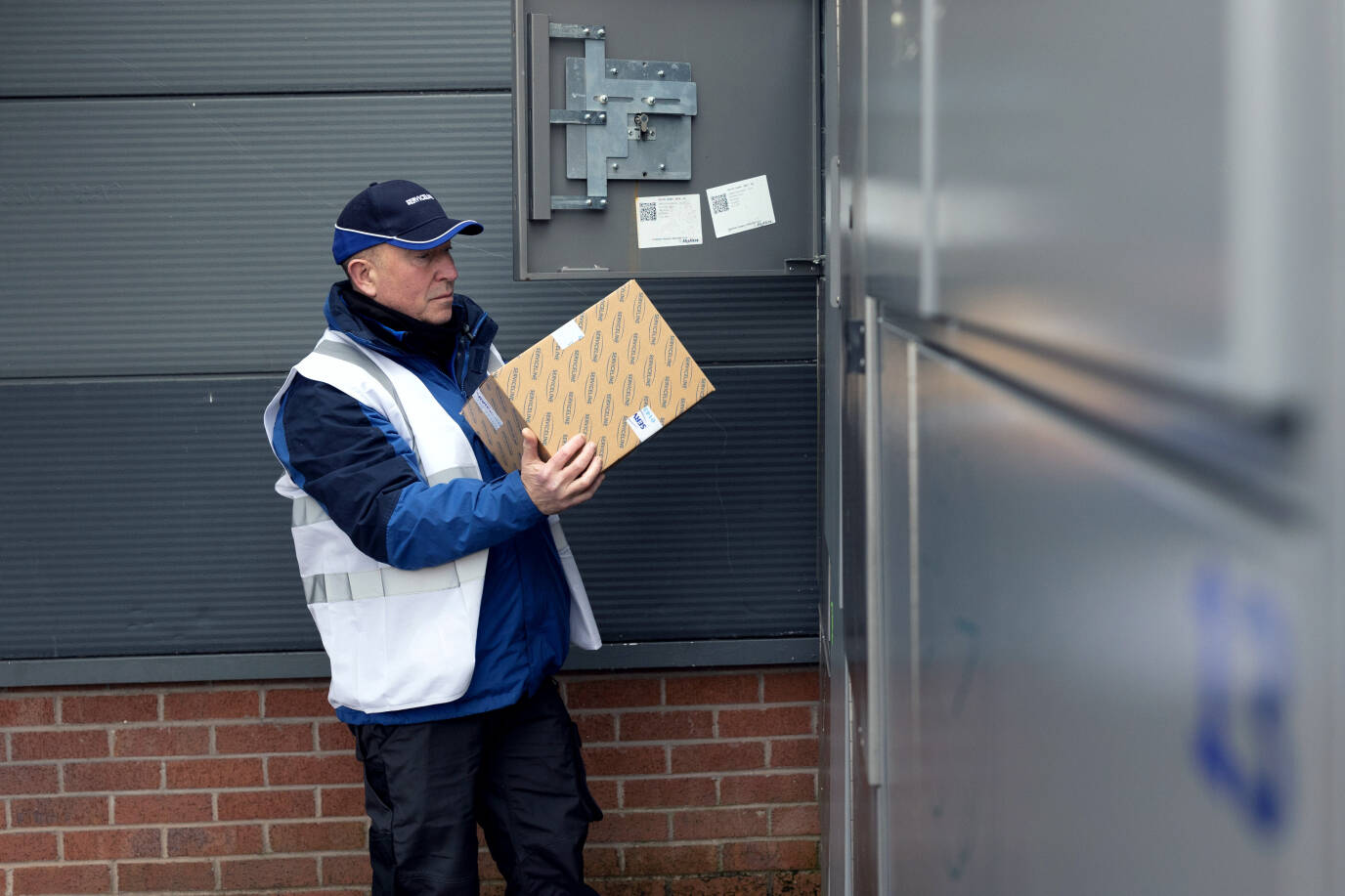





PARTS DISTRIBUTION FUNCTIONS |
---|
Reactive Engineer Van Stock Replenishment |
Reactive Engineer Central Parts Stock |
Reactive Engineer Satellite Parts Stock |
PPM & Deep Clean Van Replenishment |
Procurement |
Arrival
The First Time Pick is a measure of stock available from our central stores. In excess of 80% of parts have been available for picking by our Stores Operatives for dispatch to engineers. When parts are not available for first time picking, we will use our extensive network of suppliers, many of whom are able to ship direct to our engineers’ Bybox to ensure there is little or no delay when compared to stocked items.
Awareness and management of lead times is again critical to our ability to meet service SLAs. Lead times from all of our suppliers are constantly monitored and SLAs are in place with to ensure that we have access to the vast range of spares required to repair the equipment in stores. Lead times and usage form the basis for our minimum reorder levels which trigger replenishment orders to mitigate the risk of high use parts being out of stock.
Our Bybox network is integral to our service performance. Ensuring that our SL+1 Reactive Engineers have parts in their Bybox early morning increases efficiency and prevents delay in returning equipment in the field to a fully working status. With a 99.89% success rate, this aids in driving the overall availability.